As the heavy industries change, the requirements for refractories and their process control have also become increasingly more demanding. We at RHI Magnesita have satisfied these needs in the past and led our industry’s innovation for years now. And we are ready to take the next step: digitalization, robotics & automation, sustainable solutions and data-driven process control.
Digitalization
APO

Predict your wear lifetime with the power of AI
Highest safety standards, complete utilization of your lining’s durability, leading to no break-outs: These are just some of the requirements that you as a steelwork manager face on a daily basis. Ensuring that logistical requirements are met and ensuring a balance between inadequacies of operating personnel and technology are other necessary aspects in achieving maximum refractory performance.
E-TECH
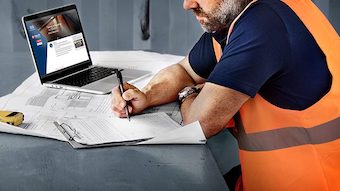
A platform to calculate and optimize your slag foaming, splashing, mass balance, etc.
Process safety
RHI Magnesita and Primetals Collab.
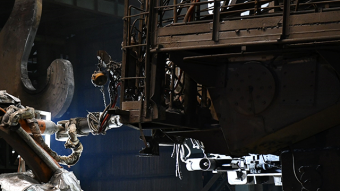
Robot, Flow Control systems and refractory elements hand in hand: RHI Magnesita and Primetals Technologies have joined forces to enable our Flow Control customers an extended offering beyond systems and refractories – industry proven robotic based automation solutions on the continuous casting area. The result is a seamless interplay of all aspects, which is adapted to your needs and thus guarantees your peace of mind.
Learn more – Smart plant concept
VISIR Ladle Hot Spot Detection
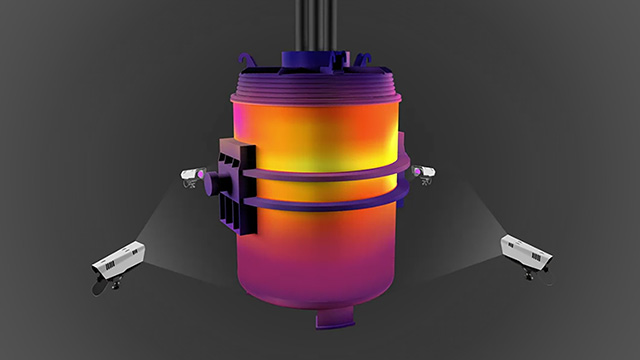
Safety comes first, especially in the steel, metal and non-ferrous industries. The risk of ladle breakouts will always be present when handling liquid metal and you have to deal with equipment damage, personnel injuries and loss of production as a consequence. Therefore, ladle refractories undergo a timely exchange, even though they could last a few more heats. We provide a solution which lets you control your ladles status and further increase the safety of your operations: VISIR – LadleSafe.
Flow Control
INTERSTOP® SX Ladle Gate

Brand new high-performance ladle gate system focused on optimising TCO and increasing safe operations.
New Argon Purging Technology

In order to achieve highest yield of prime quality products a very tight control of caster boundary conditions is required. One key aspect is to balance the application of inert gas into the casting channel. The aim should be to use smallest argon quantities possible in order to avoid sliver defects in the mould but high enough to combat alumina clogging in the casting channel being able to cast the targeted sequence length.
Learn more – New Argon Purging Technology
Sustainable & eco-friendly products
Emission-free bricks

The severity and urgency of the climate crisis have become increasingly clear. The global industry needs to rapidly adapt itself to not only improve health and safety conditions at the workplace, but also to minimize air pollution in the surroundings of Steel Plants. RHI Magnesita can support reducing fume emissions with future-oriented technology.
Learn more – Zero emissions for a better environment
Circular Economy Solution

The circular economy approach gives endless possibilities to create a thriving economy. After all, recycling solutions mean saving CO2 emissions and avoiding the unnecessary disposal of residues while restoring already extracted materials back in the economy.
Learn more – RHI Magnesita The Circular Economy Model
Automation
Terminator XL
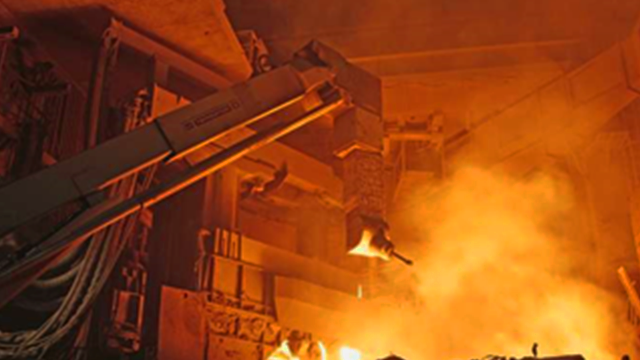
Limited heat numbers from EAF campaigns, high costs from EAF downtime, and a challenging work environment for your employees: all these challenges are present in your steel mill on a regular basis. To counteract these aspects, we have developed a gunning manipulator for highly efficient gunning repair of any part of the EAF: the Terminator XL!
Learn more – RHI Magnesita Machinery
The Shooter – Novel gunning solution for the BOF

As world’s leading refractory supplier RHI Magnesita expands its technology leadership with focused R&D projects aiming the optimization of your value chain. Besides commodities RHI Magnesita also offers system solutions for the optimum fulfilment of customer demands. Working on the BOF takes up a lot of time and can also endanger the safety of your employees. To counteract these aspects, we have developed a gunning solution for the BOF: the Shooter!